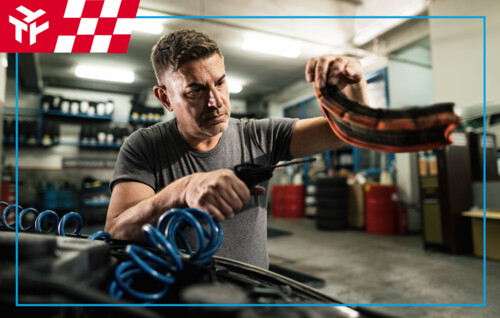
Oleje do sprężarek.
- Sprężarki – klasyfikacja i układy smarowania.
- Warunki pracy i ogólne wymagania.
- Klasyfikacja.
- Jak często wymiana oleju w kompresorze?
- Liczba kwasowa – co oznacza?
1. Sprężarki – klasyfikacja i układy smarowania
Sprężarki, znane także jako kompresory, pełnią kluczową rolę w procesach zwiększania ciśnienia sprężanego czynnika, takiego jak powietrze, gaz czy czynnik chłodniczy, do pożądanej wartości końcowej. Istotnym parametrem określającym ich działanie jest stopień sprężania, czyli stosunek ciśnienia tłoczenia do ciśnienia ssania. W przypadku potrzeby wysokiego ciśnienia tłoczenia, wykorzystuje się sprężarki wielostopniowe, gdzie gaz jest chłodzony pomiędzy kolejnymi stopniami w specjalnych chłodnicach powietrznych lub wodnych.
Sprężarki podzielone są na różne kategorie w zależności od ich zastosowania:
- Sprężarki powietrza
- Sprężarki gazowe
- Pompy próżniowe
- Sprężarki chłodnicze
Układy smarowania sprężarek są zróżnicowane ze względu na ich konstrukcję. Wykorzystują one różne techniki smarowania statycznego i hydrodynamicznego. W najpopularniejszych sprężarkach tłokowych smarowane są dwa główne zespoły części: mechanizmy (takie jak łożyska wolu korbowego i korbowodu, oraz wodziki) oraz cylindry (zawierające tłoki, pierścienie tłokowe uszczelniające, ścianki cylindrów, oraz zawory). Wprowadzenie środka smarującego do obszarów styku może być realizowane poprzez metody bezciśnieniowe (np. smarowanie rozbryzgowe, grawitacyjne) lub ciśnieniowe (np. smarowanie za pomocą wtrysku oleju).
Olej sprężarkowy pełni wiele istotnych funkcji w różnych układach smarowania, w tym:
- Zmniejszanie tarcia
- Redukcja zużycia części
- Odprowadzanie ciepła wytworzonego podczas tarcia i sprężania gazu
- Eliminacja produktów zużycia oraz innych zanieczyszczeń z układu smarowania
- Ochrona przed korozją
- Uszczelnianie komór roboczych
Dokładne zrozumienie wymagań eksploatacyjnych sprężarek ułatwia proces wyboru odpowiedniego oleju sprężarkowego, co przyczynia się do wydłużenia ich żywotności oraz zapewnienia niezawodności działania.
2. Warunki pracy i ogólne wymagania
Podstawowymi parametrami pracy, wpływającymi na jakość stosowanego oleju są: temperatura, ciśnienie i czystość sprężonego czynnika.
Temperatura pracy określa wymaganą lepkość oleju – w maksymalnej temperaturze olej musi wykazywać na tyle wysoką lepkość, aby chronić powierzchnie trące i pełnić funkcję uszczelniającą. Oleje sprężarkowe muszą się wykazywać dobrą stabilnością termiczną, ponieważ w wysokich temperaturach pracy i w kontakcie z powietrzem, olej występujący w postaci cienkiego filmu łatwo ulega destrukcji termicznej.
Nie powinny one również zawierać lotnych składników.
Temperatura zapłonu tych olejów powinna być wyższa niż najwyższa temperatura występująca w układzie sprężania. Wzrost ciśnienia powoduje wypychanie oleju z pomiędzy pierścieni tłoka i ścianki cylindra (w sprężarkach tłokowych), względnie między ścianką wirnika i łopatkami (w sprężarkach łopatkowych), stwarzając ryzyko przerwania ciągłości smarowania – przez to pożądane są również dobre własności przeciwzatarciowe oleju.
Kolejnym parametrem wpływającym na jakość oleju jest wilgoć. Im wyższa temperatura sprężanego gazu, tym wyższa jest zawarta w nim ilość wilgoci. Wilgoć może kondensować i powodować korozję powierzchni trących. Tym samym olej powinien adsorbować i usuwać z układu produkty korozji i wodę. Jeśli ilość wilgoci jest duża, olej powinien tworzyć z nią emulsję.
Do pomp próżniowych powinny charakteryzować się niską prężnością par, dobraną właściwie do parametrów uzyskiwanej próżni oraz dobrą stabilnością chemiczną i termiczną.
Oleje te najczęściej otrzymywane są z rop naftenowych, z bardzo dokładnie zrafinowanych wąskich frakcji próżniowych. Oleje wyższych klas jakościowych mogą zawierać dodatki przeciwutleniające, przeciwkorozyjne, myjące i przeciwpienne. Nie powinny zawierać polimerowych dodatków poprawiających właściwości niskotemperaturowe (depresatorów) i reologiczne (wiskozatorów), ze względu na ich skłonność do koksowania. Najczęściej stosowane są oleje mineralne.
3. Klasyfikacja
Aktualnie stosowaną klasyfikacją olejów sprężarkowych jest klasyfikacja według ISO 6743 część 3A – dotyczy ona olejów do sprężarek tłokowych i rotacyjnych oraz do mechanicznych pomp próżniowych. Należą tutaj również oleje do sprężarek gazu i sprężarek chłodniczych, których klasyfikację przedstawia norma ISO 6743 część 3B. Obu wymienionym normom lSO odpowiada równoważna norma PN-91 /C-96099/05.
Klasyfikacja środków smarowych do sprężarek powietrza wg lSO 6743-3A
- oleje mineralne z dodatkami uszlachetniającymi – sprężarki tłokowe lub rotacyjne do powietrza:
- DAA – do lekkich warunków pracy
- DAB – do średnich warunków pracy
- DAC – do ciężkich warunków pracy
- Oleje mineralne z dodatkami uszlachetniającymi – sprężarki rotacyjne łopatkowe i śrubowe do powietrza:
- DAG – do lekkich warunków pracy
- DAH – do średni warunków pracy
- DAJ – do ciężkich warunków pracy
Klasyfikacja środków smarowych do sprężarek gazów wg lSO 6743-3B
- DGA – głęboko rafinowane oleje mineralne do gazów, które nie reagują z olejami mineralnymi lub nie obniżają lepkości olejów mineralnych do stopnia uniemożliwiającego ich stosowanie – sprężarki wyporowe tłokowe i rotacyjne do gazów: N2, H2, NH3, Ar, CO2, He, SO2, H2S, CO.
- DGB – specjalne oleje mineralne do gazów zawierających wilgoć i kondensat – sprężarki wyporowe tłokowe i rotacyjne.
- DGC – oleje najczęściej syntetyczne do gazów o dużej rozpuszczalności w olejach mineralnych – sprężarki wyporowe tłokowe i rotacyjne (węglowodory, NH3, CO2 – duże ciśnienia).
- DGD – zwykłe oleje syntetyczne do gazów, które reagują chemicznie z olejem mineralnym – sprężarki wyporowe tłokowe i rotacyjne (HCl, Cl2, O2, tlen z powietrzem, CO).
- DGE – zwykłe oleje syntetyczne do gazów redukujących, bardzo suchych – sprężarki wyporowe tłokowe i rotacyjne (N2, H2, Ar – duże ciśnienia).
Klasyfikacja środków smarowych do sprężarek chłodniczych wg lSO 6743-B
- DRA – oleje mineralne naftenowe, parafinowe lub syntetyczne – sprężarki tłokowe i rotacyjne w konfiguracji hermetycznej, półhermetycznej lub otwartej, do amoniaku i chlorowęglowodorów do temperatur odparowalnika powyżej –40°C.
- DRB – syntetyczne oleje węglowodorowe – sprężarki j.w. wyposażone w instalacje z suchymi parownikami, temperatury parownika poniżej –40°C, do amoniaku i chlorowcowęglowodorów.
- DRC – głęboko rafinowane oleje mineralne lub syntetyczne węglowodory – sprężarki j.w. do temperatur parowalnika powyżej 0°C, do chlorowcowęglowodorów.
- DRD – syntetyczne oleje, które są niemieszalne z czynnikiem chłodniczym/mineralne oleje lub syntetyczne węglowodory – sprężarki j.w. typu otwartego, do zastosowań, gdzie olej i czynnik chłodniczy nie mogą się mieszać i muszą szybko się separować
- DRE – oleje syntetyczne typu estrów mieszalne z czynnikiem chłodniczym
4. Jak często wymiana oleju w kompresorze?
Producenci sprzętu zazwyczaj jasno określają czas, po którym należy wymienić olej do sprężarki. Często czynność wykonuje się np. po 500 godzinach pracy. Należy wtedy spuścić zalegające powietrze, odłączyć urządzenie od prądu, a następnie rozmontować obudowę sprężarki, wyczyścić zbiornik i usunąć stary olej. Po złożeniu części wystarczy tylko wlać nowy olej i sprawdzić pracę urządzenia po wymianie. Producenci zalecają też dość często czyścić filtr powietrza (np. raz w tygodniu). Z zaworu pod zbiornikiem należy usuwać regularnie zbierającą się wodę. Cały zbiornik czyści się raz na pół roku.
5. Liczba kwasowa – co oznacza?
Liczba kwasowa dla olejów sprężarkowych, hydraulicznych i przekładniowych jest jedną z charakterystycznych wartości. Jest to ilość zasady, wyrażona w miligramach wodorotlenku potasowego (KOH), niezbędna do neutralizacji (zobojętnienia) wszystkich kwasów zawartych w 1 gramie produktu, przy miareczkowaniu w znormalizowanych warunkach oznaczania. Oznacza się ją według normy PN-ISO 6618:2011. Oznaczenie liczby kwasowej polega na miareczkowaniu roztworu odważonej ilości badanej substancji, w rozpuszczalniku zawierającym wskaźnik. Jako rozpuszczalnik jest stosowany roztwór zawierający toluen (500 ml), alkohol izopropylowy (495 ml) i wodę (5 ml). Miareczkowanie jest wykonywane mianowanym alkoholowym roztworem wodorotlenku potasu (KOH), potencjometrycznie lub wobec wskaźnika.